Quality
- Related ESG :
- S G
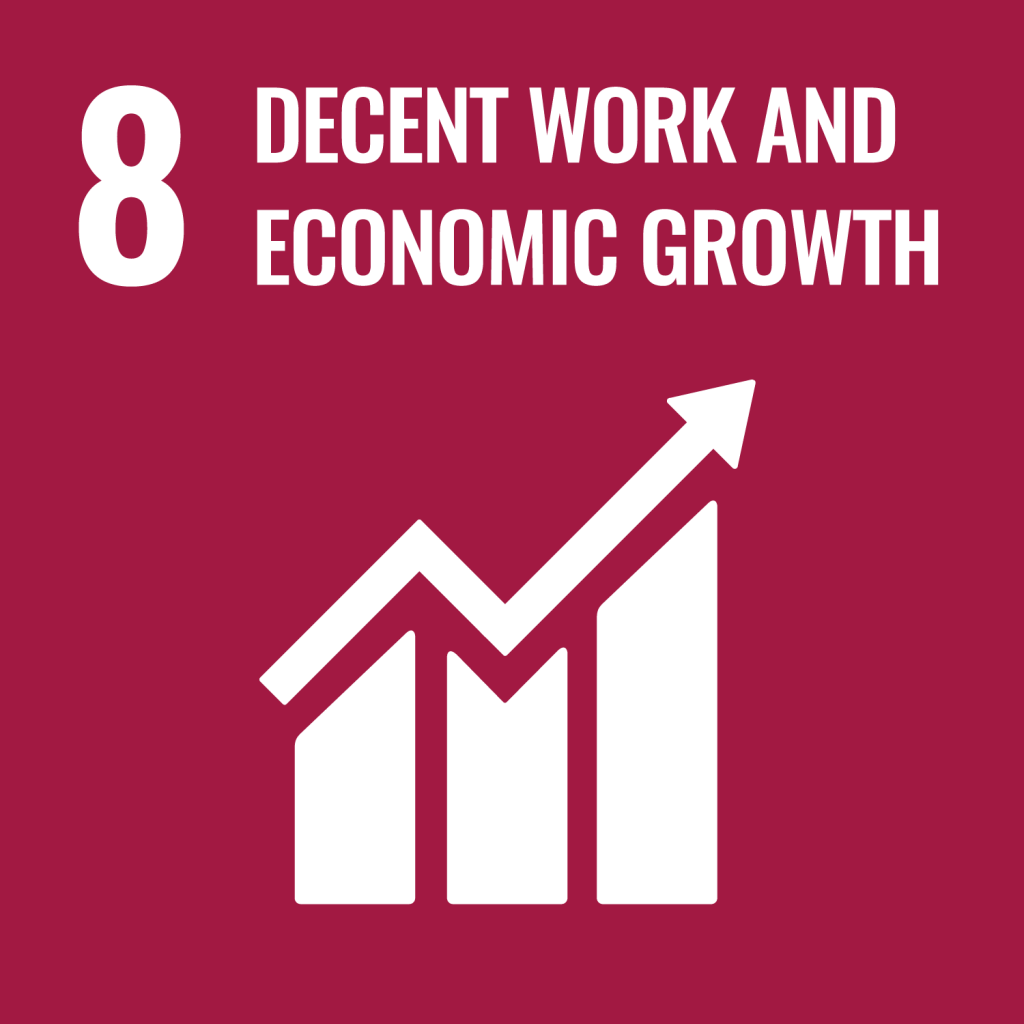
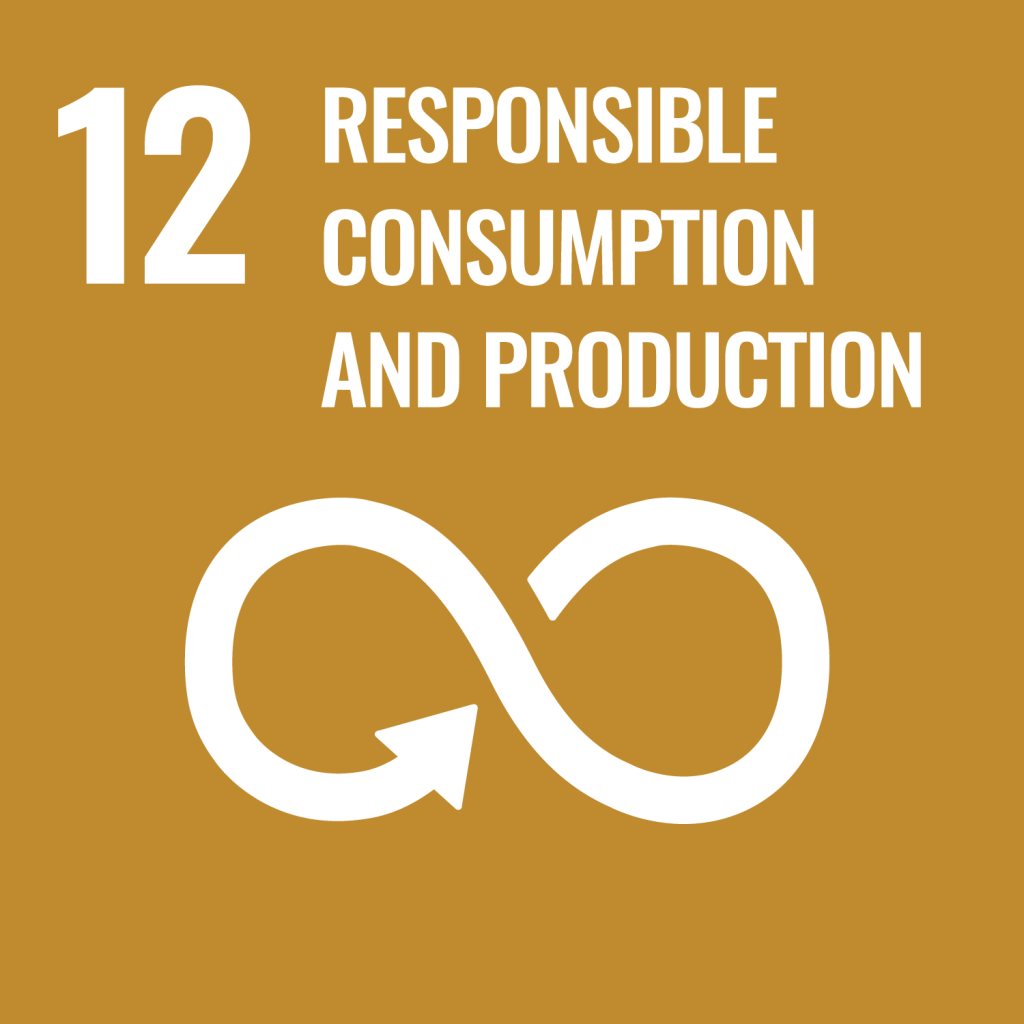
Management approach
Policy and approach
Toyobo group is striving to ensure customer satisfaction and win customers' trust, not only through the safety of our products and services, demonstrating concern for the environment, and maintaining compliance with relevant laws and regulations, but also through high quality standards. In order to achieve this, we have formulated The Toyobo Group’s Basic Policy on Product Safety and Quality Assurance. To safeguard the quality and safety of the products and services that we provide, we have established an appropriate management system, we perform quality inspections using suitable procedures, and we also strive to ensure that data is properly handled.
< The Toyobo Group’s Basic Policy on Product Safety and Quality Assurance >
- Product Safety and Quality Assurance Principle
The Toyobo Group will strive to provide products and services that satisfy and earn the trust of society, consumers, and customers.
- We will ensure all employees have a keen awareness of the need to prioritize quality while keeping the customer’s perspective in mind.
- We will provide products and services that meet the changing needs and expectations of the times, that are useful to society, and that give due consideration to the safety and protection of the environment and information.
- Activity Policy for Product Safety and Quality Assurance
- (1)
- Comply with all applicable laws and regulations
We will comply with all relevant laws, regulations, standards, and norms in relation to the safety of our products and services. - (2)
- Ensure product safety
We will ensure the safety of our products and services not only for their intended use but also against any reasonable, foreseeable misuse.
We will also strive to improve safety by voluntarily setting higher safety standards when necessary. - (3)
- Establish a system for promoting product safety
We will promote product safety and quality assurance throughout the product lifecycle, from development, design, manufacturing, sales, use and disposal, as well as throughout the supply chain. - (4)
- Protect and provide information appropriately
We will strive to protect all confidential information obtained through any
product safety and quality assurance activities as set forth in the Toyobo Group
Privacy Policy.
We will also proactively provide relevant information to stakeholders whenever
appropriate. - (5)
- Promote education and awareness
We will promote awareness of product safety and quality assurance through education and awareness activities of all employees, including officers.
Structure
Our group has established a Quality Assurance Division Conference to oversee product liability (PL) and quality assurance (QA). In this conference, executives overseeing quality, the Quality Assurance Department General Manager in charge of business divisions, and members of the Quality Assurance Management Department meet every month. We also plan to convene the PL/QA Promotion Committee, composed of members at the business division General Manager level, six times a year, and did so in FY2023.
We have established the Quality Assurance Division as one of the measures to prevent recurrence of inappropriate conduct. Under the division, we have placed the Quality Assurance Management Department, and also the Quality Assurance Departments which are in charge of the division. By establishing the independence of the quality assurance related departments, a function which was previously implemented in each business division, we have strengthened its control over the business divisions. In addition, the Quality Assurance Management Department has been given the authority to guide and suspend the development, production, and sales of the company and group companies regarding product safety (PS) and QA of Toyobo group, and we are working to construct an appropriate quality management system and strengthen governance.
QA structure (As of April 2024)
Targets and KPIs
< Targets >
- We will increase customer satisfaction by practicing quality management throughout our entire supply chain, including upstream areas, and ensuring quality that can be trusted.
< KPIs and results >
Initiatives | KPIs | Targets | Results (FY2024) |
---|---|---|---|
|
|
0 incidents per year | 0 incidents |
|
100% | 100% |
- Incidents related to products: Defined according to internal standards based on the defintion stipulated by the Ministry of Economy, Trade and Industry
Initiatives
QA initiatives
Employees have shared access to the Quality Assurance Manual, which describes the basic approach and code of conduct for all employees when implementing Toyobo group's development, production and sales activities, and use it as the basic philosophy for Toyobo group manufacturing.
We have multilingualized our Quality Assurance Manual and deployed it to each location in countries. We also hold study sessions using the digest version to deepen understanding of manufacturing in our group.
We have further set out Quality Assurance Guidelines and are taking action to build systems that can guarantee quality.
From FY2022, we have conducted quality assurance reviews led by the head of the Quality Assurance Division to assess the quality assurance initiatives of business divisions, with the aim of strengthening quality assurance systems and governance. These reviews have clarified quality issues, while interim reviews are conducted to monitor progress in improvements.
We have enhanced our QA systems for products and services to ensure quality and product safety at every stage. In addition, our Quality Assurance Guidelines undergo rigorous scrutiny by business managers, relevant stakeholders both inside and outside the company, and specialists. This thorough review aims to prevent accidents or disruption in markets.
November was once again designated as Quality Month for FY2022. During this period, key initiatives included disseminating quality assurance messages from the president and division heads, along with displaying Quality Month posters and digital signage across all sites. We held PL/QA seminars, and reviewed quality-related misconduct at individual workplaces in accordance with the Compliance Manual.
Overview of QA initiatives
Product safety promotion activities
For each department and group company, we conduct PL/QA assessments carried out by the Quality Assurance Division, which has been made independent of the business divisions, or by QA personnel from different departments, to verify and improve PS activities. Moreover, we have established criteria for assessing PL and PS risk, and based on these criteria, we carry out inspections at each stage, from product development to sales, striving to reduce risk.
All possible measures are taken to ensure PS, and training drills are also conducted on a regular basis at all business divisions based on PL incident scenarios. PS remains a crucial theme throughout the whole of the group, and we will continue to mitigate risk as much as possible and strive to fulfill our social responsibility.
PL response system
Product safety and quality assurance education
We implement PS and QA education not only for new employees and new managers, but also for other employees at each level.
Name of seminar | Number of times held | Target / purpose | Notes |
---|---|---|---|
Seminar on basics of quality assurance | 4 times per year | Education for new employees and department-specific education | Packaged into e-learning format |
Qace seminar* | 4 times each in the first half and the second half of the year | Development of core human resources for quality control and quality assurance, and construction of an in-house human resource network for quality | Launched in FY2023 |
Training in case studies involving quality irregularities | 10 times per year | Training involving quality irregularities | Launched in FY2023 |
Education on cases of quality irregularities | 43 times per year | Education to raise awareness about the importance of eliminating quality irregularities by introducing past cases | Launched in FY2024 |
- "Qace" is an acronym formed from "Qa_assurance," "Qc_control," and "Qe_ensurance."
Name of seminar | Month held | Target / purpose | Theme in FY2024 |
---|---|---|---|
PL/QA seminar | November | Held as a component of quality assurance in which all employees participate | Activation of individuals and organizations |
Quality management seminar | January | Held as an opportunity for top management to consider quality management | Problem-solving through data science and its standard scenarios |
ISO 9001 Certification Status
Response to the improper quality incidents
Toyobo group is responding to the improper quality incidents discovered related to the PLANAC® and other engineering plastics in 2020 by firmly establishing “manufacturing that fulfills our promise to provide safety and security from the customer’s perspective” and by fortifying the inspection and quality confirmation mechanisms in the group’s risk management system.
Status of the engineering plastics department
Following improper quality incidents involving PLANAC® and other products, we have individually contacted our customers and reacquired Underwriters Laboratories (UL) certification for most of our products.
We also proceeded to investigate the status of all our products through questionnaires and other methods. Any improper quality incidents in the Engineering Plastics Department deemed serious issues, such as violations of agreements with customers, were individually reported to all affected customers and addressed.
Based on our investigations and customers’ cooperation with confirmations, we have not identified any serious defects in product safety or basic functions. Through the establishment of robust quality control systems and enhanced governance, we are dedicated to rebuilding trust in our company.
Additionally, we regained ISO 9001 certification, which had been revoked due to these incidents, from Lloyd’s Register Quality Assurance Limited (LRQA) in May 2024.
Lifting of the FDA Warning Letter at Otsu Pharmaceuticals Plant
On August 19, 2021, Toyobo received a Warning Letter from the U.S. Food and Drug Administration (FDA) regarding the quality management procedures of pharmaceutical manufacturing processes at the Otsu Pharmaceuticals Plant (Otsu City, Shiga Prefecture). Since then, we have been working closely with the FDA to address the issues identified.
Following an inspection by the FDA in February 2023, we received a Close-out Letter dated July 5, 2023 regarding the lifting of the Warning Letter. Moving forward, we will continue to maintain close collaboration with the FDA, dedicating our efforts to improving and strengthening our production and quality management systems.
Our goal is to strive towards being a contract manufacturer that contributes to providing high-quality pharmaceutical products needed by patients worldwide.
Strengthening the quality risk management system
The company responded to the improper quality incident by adopting a “three lines of defense” structure at the start of fiscal 2021. The multi-layered structure for detecting and preventing quality-related misconduct positions the business divisions as the first line of defense and the Quality Assurance Division and Internal Audit Department as the second and third lines of defense.
The Quality Assurance Division, which is the second line of defense, identified improper inspections and other items as significant quality-related risks, and led and assisted risk assessments at each business unit. The division formulated measures to reduce risk and has begun assisting in the application of the measures.
The Internal Audit Department, the third line of defense, created a Risk Management Audit Team to perform quality audits for the first and second lines of defense. The department collects information on the operation status and current issues of the Quality Assurance Division and the business divisions, and examines the best approach to coordinating audits.
In the second half of fiscal 2021, the Internal Audit Department began a first line audit with the Quality Assurance Division. The department also audited the Quality Assurance Division and had a frank dialogue with the division about expectations for its supervision of each business division.
We also implemented data integrity (DI) measures related to quality, including automating the inspection report processes of each business division’s Quality Assurance Departments to reduce human error, among other initiatives.