Safety, Disaster Prevention
- Related ESG :
- E S G
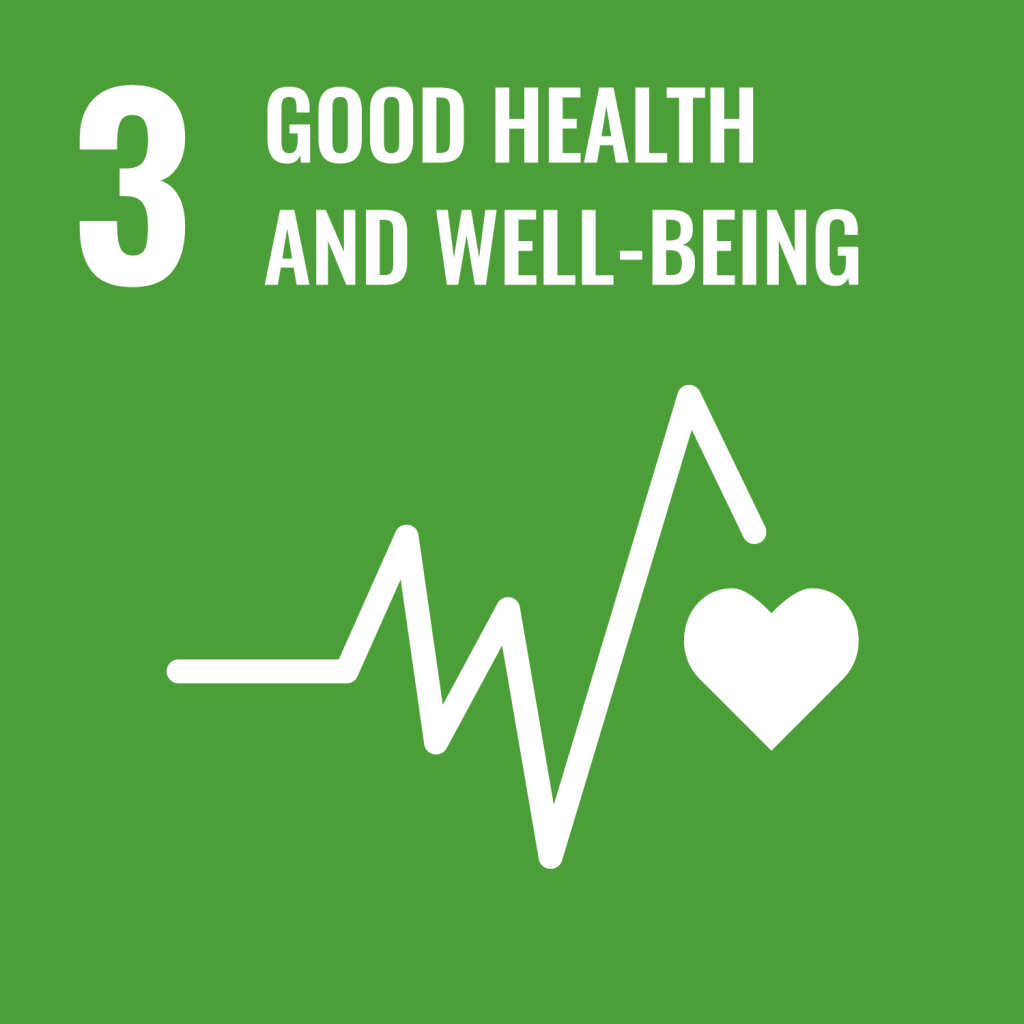
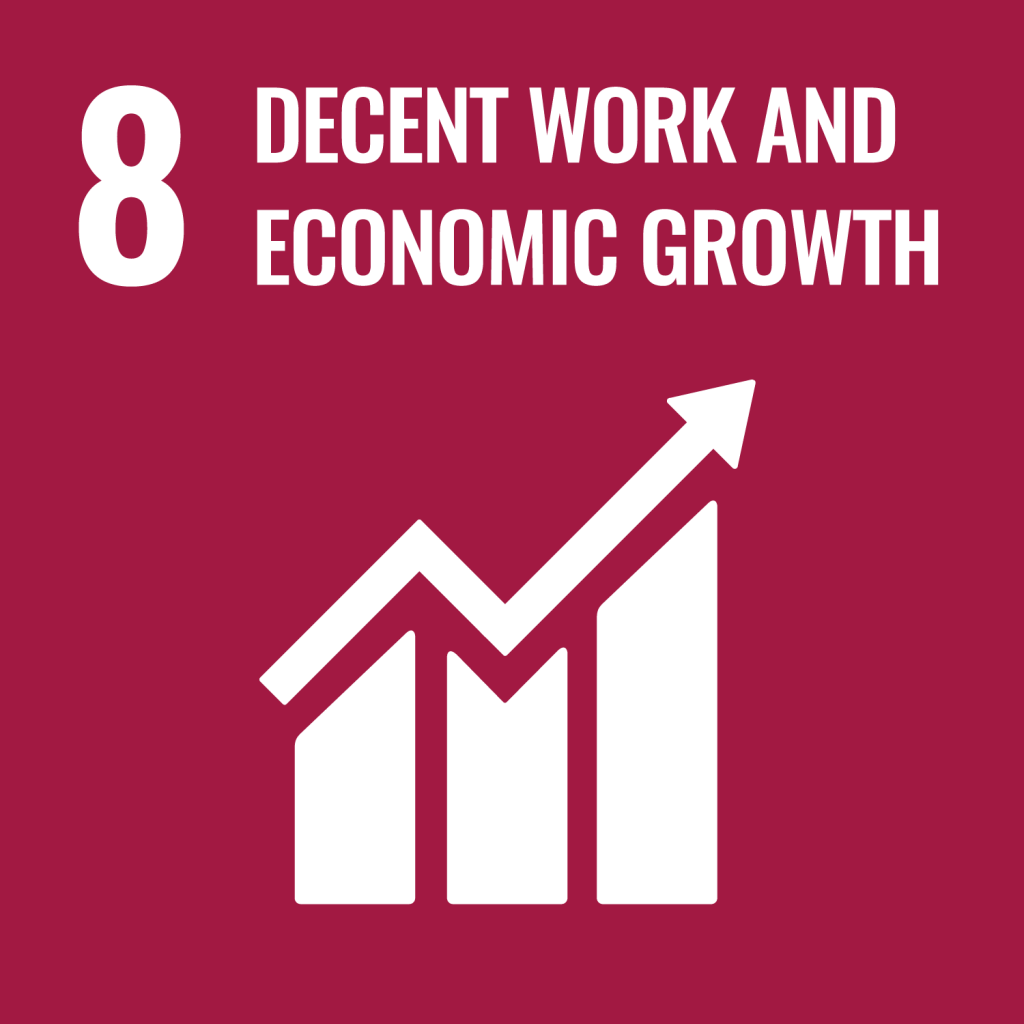
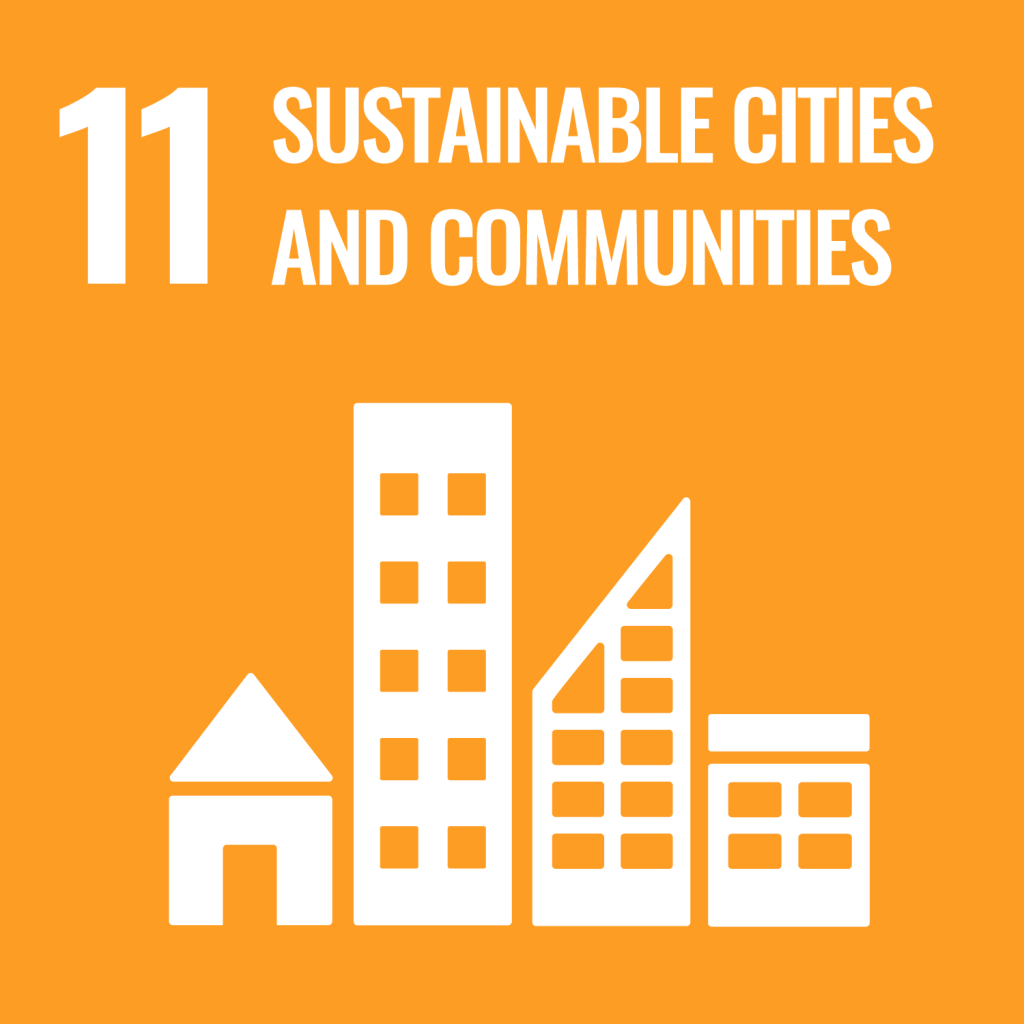
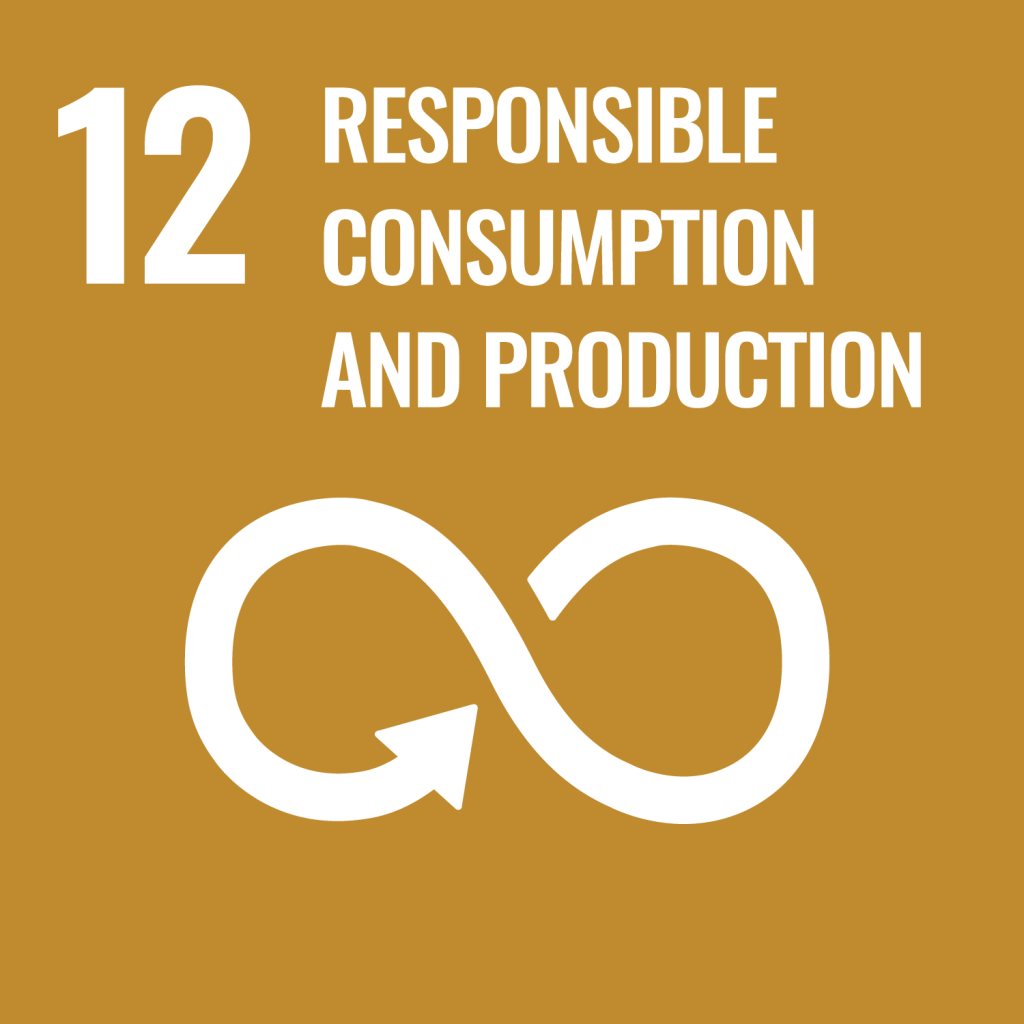
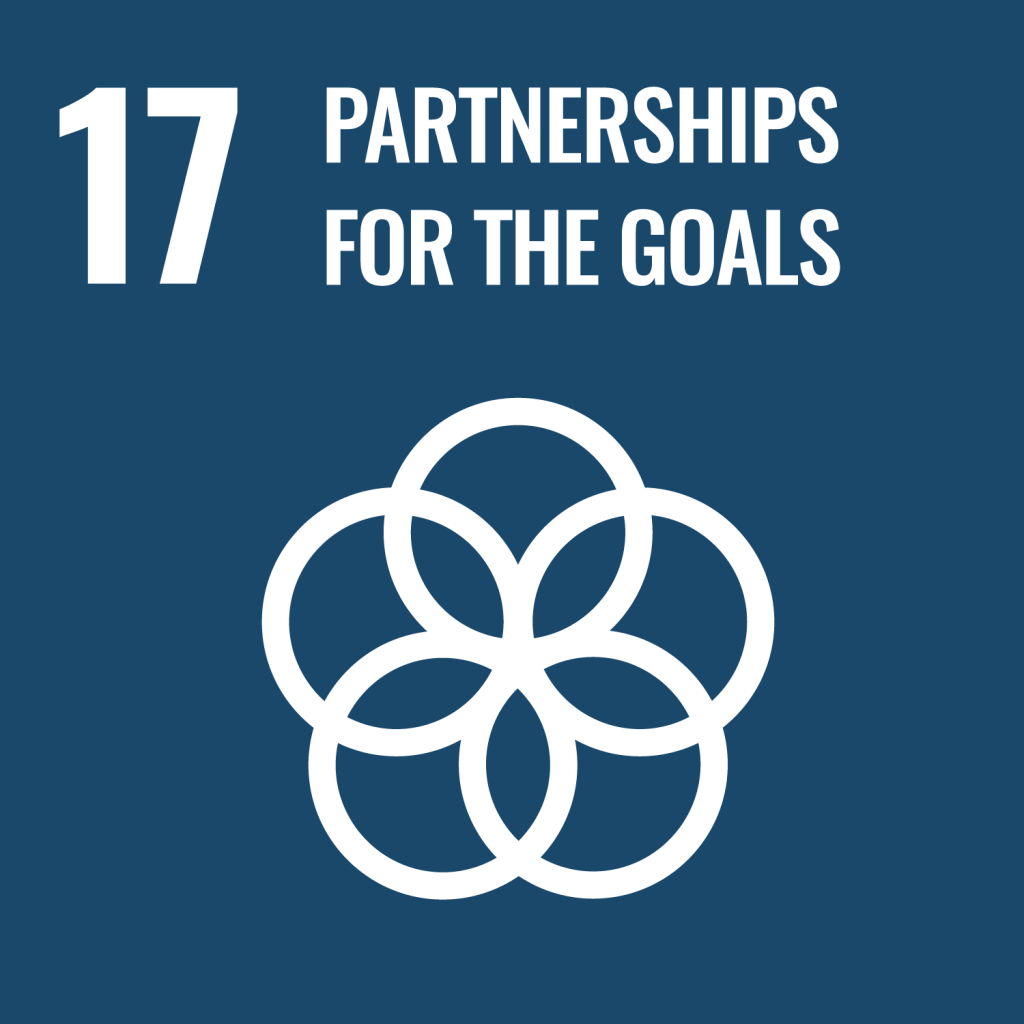
Management approach
Policy and approach
Toyobo group recognizes that ensuring health and safety is a precondition for corporate activities. We have formulated the Toyobo Group Basic Policy on Health & Safety, which applies not only to our employees but also to the personnel of partner companies (contractors), and we are striving to build a safe workplace environment.
Our safety declaration, instituted in April 2022, states that “We will ensure ‘safety first’—occupational safety, environmental safety, product safety, and equipment safety.” Our slogan in FY2024 was “Protect yourself, protect your colleagues, and speak up when noticing something,” and it remains the same in FY2025.
Toyobo group designates September as “Disaster Preparedness Month” and September 6 as “Toyobo Group Disaster Preparedness Day,” when we conduct awareness-raising activities related to preparedness for fires and other disasters.
We do so out of a powerful determination to never forget the fatal fires that occurred at the Tsuruga Research and Production Center (No. 2 Plant) on September 6, 2018, and the Inuyama Plant on September 27, 2020, and to never allow the lessons learned from these to fade away.
We are committed to creating fire-resistant workplaces and developing personnel with the competence to securely prevent fires, aiming to rebuild trust from society by establishing robust production sites.
< TOYOBO Group Basic Policy on Health & Safety >
- Health & safety principle
Based on the concept that ensuring safety and sanitation is a major premise for business activities, we will actively work to ensure the safety of employees, enhance the cleanliness of working environments, and improve health under the spirit of respect between people with the aim of creating cheerful, happy workplaces and a prosperous society.
- Policy for health & safety activities
- (1)
- Ensuring workplace safety
Toyobo group works to enhance the safety and security of environments at its workplaces with the aim of achieving zero accidents. - (2)
- Enhancing environmental sanitation and improving health
Toyobo group is enhancing the sanitation of environments at its workplaces and working to improve the health of its employees with the aim of realizing happy workplaces. - (3)
- Compliance with social norms
Toyobo group complies with social rules and works to realize a prosperous society and communities with which the company can coexist.
Structure
To ensure steady progress in safety and disaster prevention initiatives, which are among our most important management issues, we have established the Safety and Disaster Management Division.
This division reports directly to the President and possesses a high degree of decision-making authority.
The Head of the Safety and Disaster Management (S&DM) Division, who is also the Representative Director and Senior Managing Executive Officer, leads the Safety and Disaster Management Conference. This conference includes experts from various fields as its members. During these meetings, the members evaluate the effectiveness of safety and disaster management activities and draft company-wide policies, which are then finalized by the Sustainability Committee. The conference also reports on progress to the Board of Directors as appropriate.
Under the SD&M, the Environment, Safety and Disaster Management Department plans and advances safety and disaster management activities. It also hosts the Safety and Disaster Management Promotion Conference, which is composed of representatives from each department. This conference handles discussions, decision-making, and progress on specific matters based on established policies. It also organizes teams of members and a chairperson to visit the company’s business sites, factories, and group companies to conduct safety and environmental assessments and to inspect local activities. To address fire and explosion risks in particular, we perform periodic on-site management inspections through third-party experts.
Furthermore, each production center, plant, and research center has its own Health and Safety Committee. These committees, composed of employee representatives, managers and experts, investigate and deliberate on matters relating to employee safety, disaster prevention, and health, including the status of risk assessments, at each workplace.
Labor union representatives also participate in the discussions of the Safety and Disaster Management Promotion Conference and the Health and Safety Committee.
Toyobo group structure for safety, disaster prevention, and the environment
Targets and KPIs
< Targets >
- We will strive to prevent disasters and accidents by clarifying and thoroughly complying with basic safety throughout the entire Toyobo group.
< KPIs and results >
Initiatives | KPIs | Targets | Results (2023) |
---|---|---|---|
|
|
|
|
|
|
|
|
|
|
|
|
|
|
|
- Major accidents: Defined according to internal standards based on the definition stipulated by the Ministry of Health, Labour and Welfare
Initiatives
Safety initiatives
Under the TOYOBO Group Basic Policy on Health & Safety, we are implementing the following occupational safety initiatives.
Making people, equipment, and processes safer
We identify sources of serious hazards and enact measures to prevent major accidents. Specifically, we use risk assessments and work research to assess on-site risks, then make improvements to equipment and work processes. We are also making efforts to prevent accidents by incorporating those improvements in procedure manuals and by educating employees. When an accident occurs at other companies or workplaces, we review the incident as a case study to prevent the occurrence of similar accidents, while checking for and addressing similar risks in our own workplaces.
In new businesses and projects, we conduct preliminary investigations and risk assessments related to occupational health and safety prior to capital investment, and have established and are operating a system to review the effectiveness of countermeasures.
We issue “Safety and Disaster Prevention News.” Using the lessons from accidents and disasters that have actually occurred in the past, it helps to spread awareness by providing easy-to-understand explanations, supported by illustrations, regarding key points to note to conduct operations safely, and how to respond in the event of an accident. These are becoming widely used as tools for dialogue at workplace safety meetings, and back issues of the documents are available on our company intranet for viewing at any time.
In production centers where the foreign technical training system (overseas trainees) is in operation, we have assigned instructors to provide Japanese language education and support for daily life to ensure the safety and livelihood (communication) of the trainees.
As an example, for trainees to work safely, we devise ways to make it easier for them to understand, such as translating the standard operating procedure (SOP) and using hiragana to write the reading kana.
Promotion of disaster prevention
In order to learn from the fire that occurred at our plants and empower employees to protect their own workplaces in the event of a fire, we revised the content of our fire drills to make them more practical and enabled participation in drills by all employees, including those of cooperating companies, at least once a year. For group companies inside and outside of our business sites, we advance these activities under our group policy and are gradually expanding the number of targeted companies.
Together with people at workplaces, we promote steady actions to strengthen disaster prevention, with the aim of creating worksites that prevent fires from occurring and that, in the event a fire does occur, prevent personal harm and minimize other damage. Toward that end, we have established guidelines for fire prevention equipment and standards for disaster prevention management to reduce the risk of fires. To address fire and explosion risks, we perform periodic inspections of on-site management through third-party experts.
With regard to natural disasters, we will continue to implement disaster mitigation measures by reinforcing buildings against earthquakes, improving office and plant infrastructure, and conducting emergency response drills.
3S activities and training
We undertake 3S (sort, sweep, and standardize) activities, which are the foundation for safety and disaster prevention activities, on a company-wide basis. We have put in place a safety and disaster prevention training system that is shared throughout the company, and we provide the safety and disaster prevention training that is needed at each level.
In addition, with the aim of realizing effective safety and disaster prevention knowledge training, we have installed Disaster Prevention Training Workshops—training spaces in which panel exhibition plays a central role—in all production centers, and we have established Disaster Prevention Experience Training Facilities at key sites.
Utilization of facilities for experiential safety and disaster preparedness training
To review past disaster incidents and prevent them from fading into obscurity, disaster prevention training centers have been established at the Tsuruga Research and Production Center, the Iwakuni Production Center, and the Inuyama Plant. These facilities aim to enhance knowledge and awareness of safety and disaster prevention, allowing participants, from both within and outside the company, the opportunity to experience the severity of disasters through simulated equipment.
These facilities provide a range of experiences, from common scenarios like slips and falls during walking, which are widespread nationally as well as within our group, to incidents involving falls from steps and platforms, accidents where individuals are pulled into machinery, and the challenges of dealing with smoke and evacuations during fires. Additionally, they simulate the risks associated with fires and explosions caused by dust and static electricity. The centers also share case studies of accidents that have occurred in Toyobo group in the past through digital signage and other means, providing a platform for trainees to gain fresh insights into safety and disaster prevention.
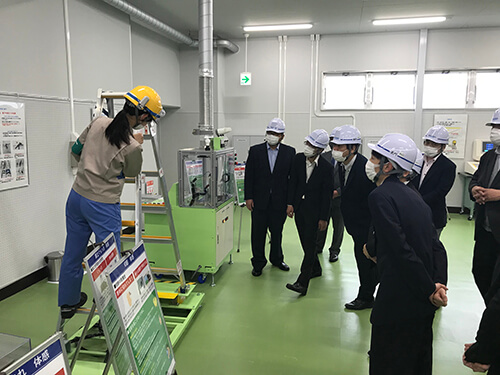
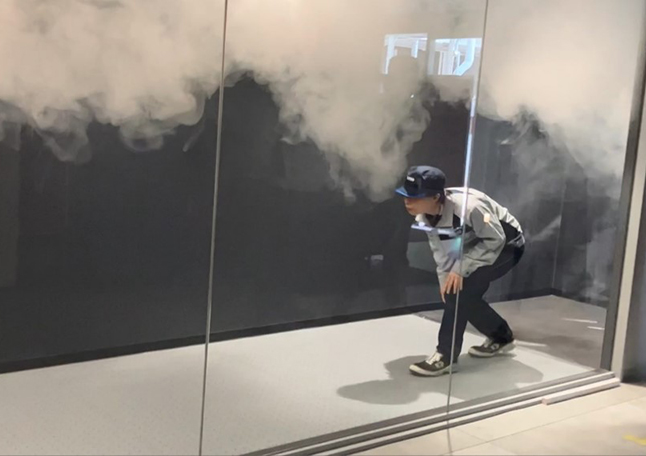
Frequency rate of lost workday injuries (Japan)
Toyobo group is striving to achieve zero accidents in accordance with the TOYOBO Group Basic Policy on Health & Safety. We place importance on the frequency rate of workplace accidents resulting in lost workdays*1. This was 1.15 in 2023, including affiliated businesses at the same business site.
For each lost time accident, case studies are conducted to determine the cause of the occurrence and countermeasures are taken.
The main types of accidents and their countermeasures are as follows.
(1) Caught in machinery: Installation of protective covers and establishment of a system for certified work
(2) Contact with hazardous materials: Selection of appropriate protective equipment and retraining in its use
(3) Falls: Improvement of aisles and plots, review of work methods
The cases are horizontally disseminated throughout the entire Toyobo Group to prevent the recurrence of similar accidents at each site.
We have set a goal of zero major incidents*2 as a KPI, we achieved zero major accidents.
- Frequency rate of workplace accidents resulting in lost workdays refers to the rate of accidents resulting in lost workday injuries per one million hours worked
- Major accidents: Defined according to internal standards based on the definition stipulated by the Ministry of Health, Labour and Welfare
Acquisition of occupational safety and health management system certification (ISO45001)
We are pursuing ISO45001 certification to conform with requirements for an occupational safety and health management system, aiming to mitigate risks in our working environments. As of March 31, 2024, we have obtained certification at three sites: the Tsuruga Research and Production Center, the Iwakuni Production Center, and the Utsunomiya Plant. We plan to continue obtaining certifications at our other production centers and plants.
Fire prevention measures (FY2024)
In the wake of the September 2018 fire accident at the Tsuruga Research and Production Center (No. 2Plant) and the September 2020 fire accident at Inuyama Plant, Toyobo group is taking two main approaches to improving safety prevention. We are fostering a culture of safety by clearly establishing safety as the highest priority and revising our education structure. We are also fortifying our safety infrastructure by formulating a plan to enhance our safety and disaster prevention equipment and management and by developing specific PDCA cycles.
Fostering a culture of safety
We had always emphasized that “safety is the highest priority” at our worksites. However, we recognized that insufficient management involvement had been a problem. To foster a deeply ingrained culture of safety, in April 2022 we introduced the New Safety Declaration. This declaration clarifies for all employees our commitment to prioritizing safety in occupational labor, as well as in relation to our products and equipment, and the environment.
Measures to enhance our awareness of safety issues include restructuring the position-based safety education system and introducing safety workshops for top management and educational programs for managers conducted by external organizations.
A safety workshop for top management was held in December 2021 , where company executives had the opportunity to study safety practices at different companies. We have held safety workshops for newly appointed officers and group company presidents since FY2023, a practice that continues to this day.
In November 2022, we conducted a survey of safety awareness among top management, Toyobo employees, and employees of cooperating companies involved in production to assess safety awareness within their respective organizations. The survey targeted 7,525 individuals, achieving a response rate of 93%. Strengths and weaknesses in every aspect of organizational structure, business operations, and leadership related to safety were visualized. Drawing on the survey findings, we are advancing activities to address weaknesses and enhance the safety culture across the organizations.
Fortifying for safety infrastructure
To address delays in funding and implementing safety and disaster prevention measures due to a focus on short-term budgets in business operations, in FY2022 we formulated the Medium-Term Management Plan for Safety and Disaster Prevention.
Working with external specialists, we created detailed risk maps for 29 sites, including domestic group companies , and evaluated the natural disaster risks for each location. We are integrating this information into future workplace planning while advancing disaster preparedness measures.
Additionally, we conducted assessments of disaster prevention capabilities at all business sites and identified areas requiring improvements to mitigate the spread of fires. As a result, we plan to invest an additional ¥18.6 billion across the group, with completion of these measures scheduled for FY2026.
We have also initiated the Disaster Management Project, aimed at establishing comprehensive disaster prevention management mechanisms. Specifically, we consulted experts to develop group-wide standards for fire prevention management. These standards are designed to align with actual conditions, enabling on-site self-inspections. Additionally, we have implemented a system where specialists conduct regular checks on operational conditions at workplaces.
Key issues in FY2025
In FY2025, we will advance initiatives with the following set as key issues:
- Deployment of safety and disaster prevention activities with participation by all employees
- Prevention of recurring occupational accidents
- Enhancement of hierarchy-specific training
Steps to enhance our culture of safety
- This expression is a quote from the dss+ Bradley curve of the stages of safety culture development