Plastic Resource Circulation
- Related ESG :
- E
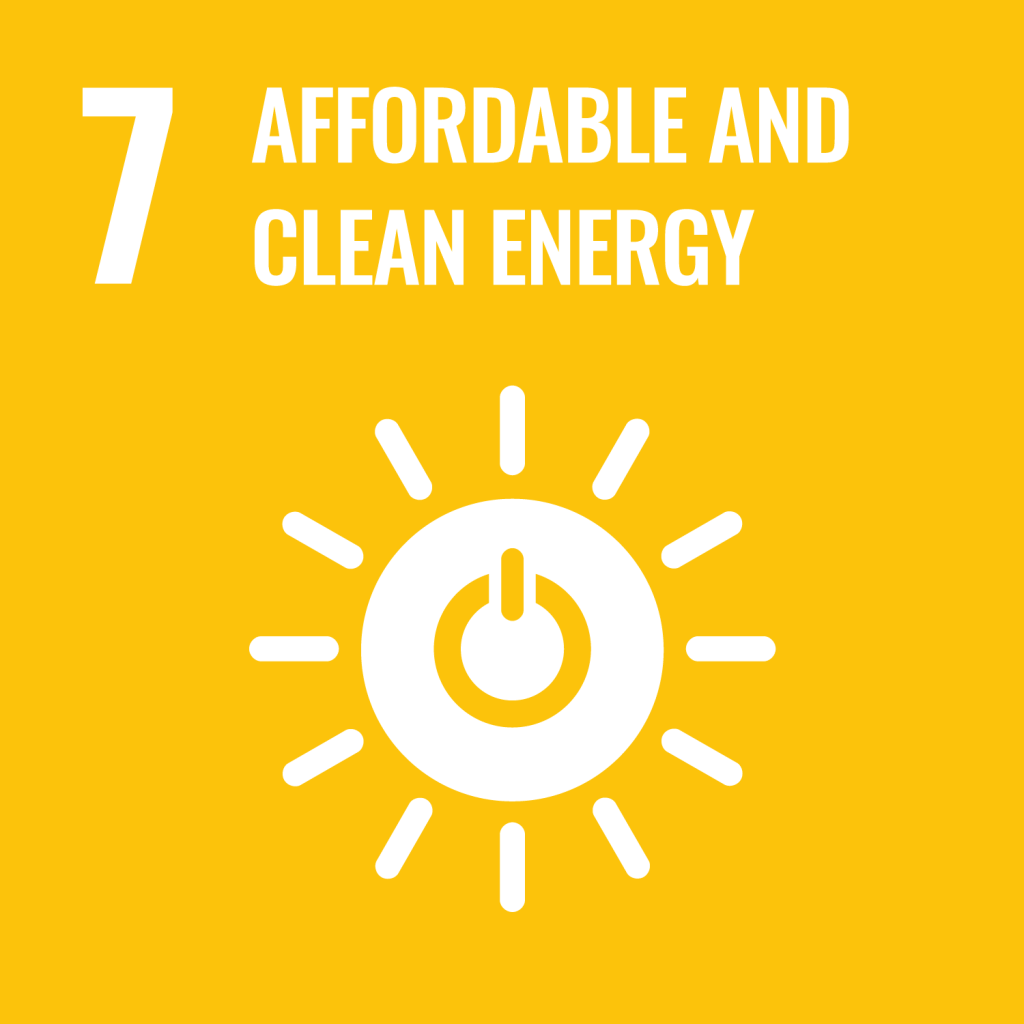
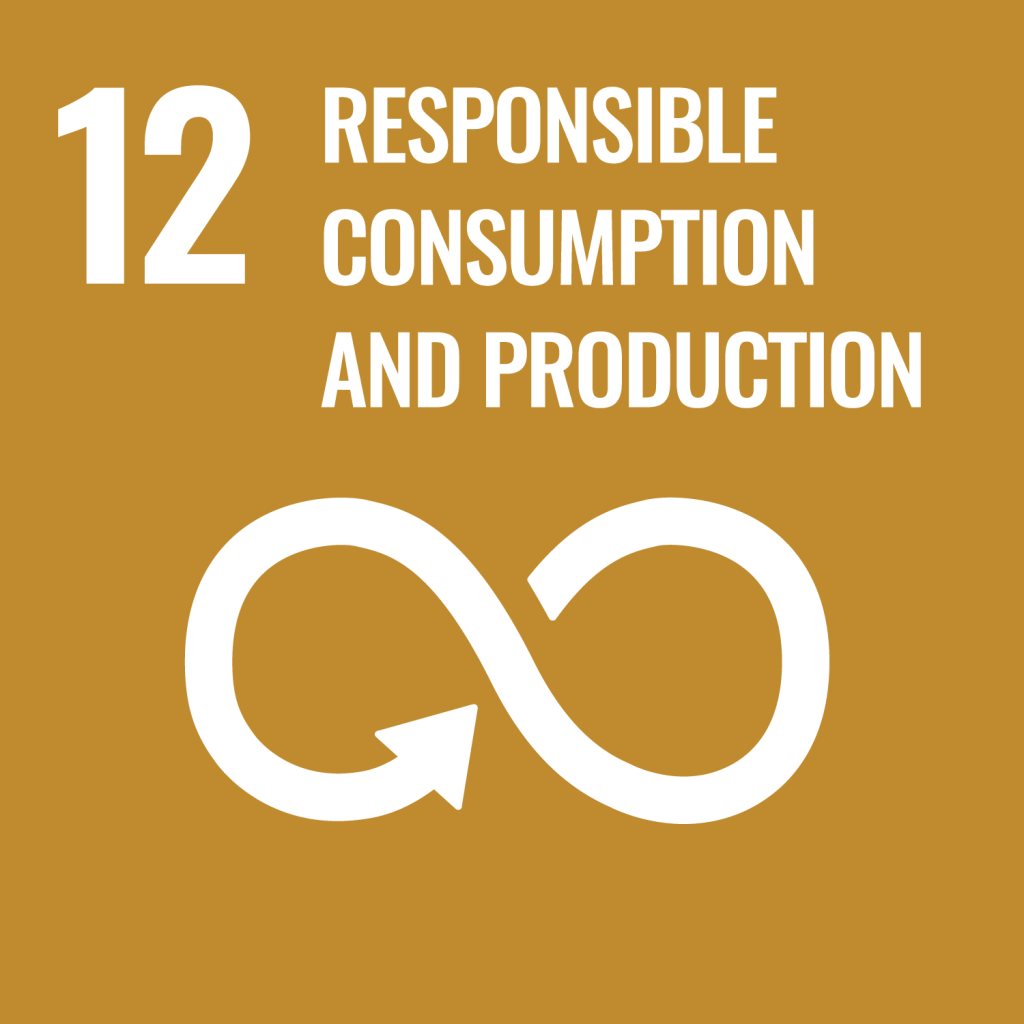
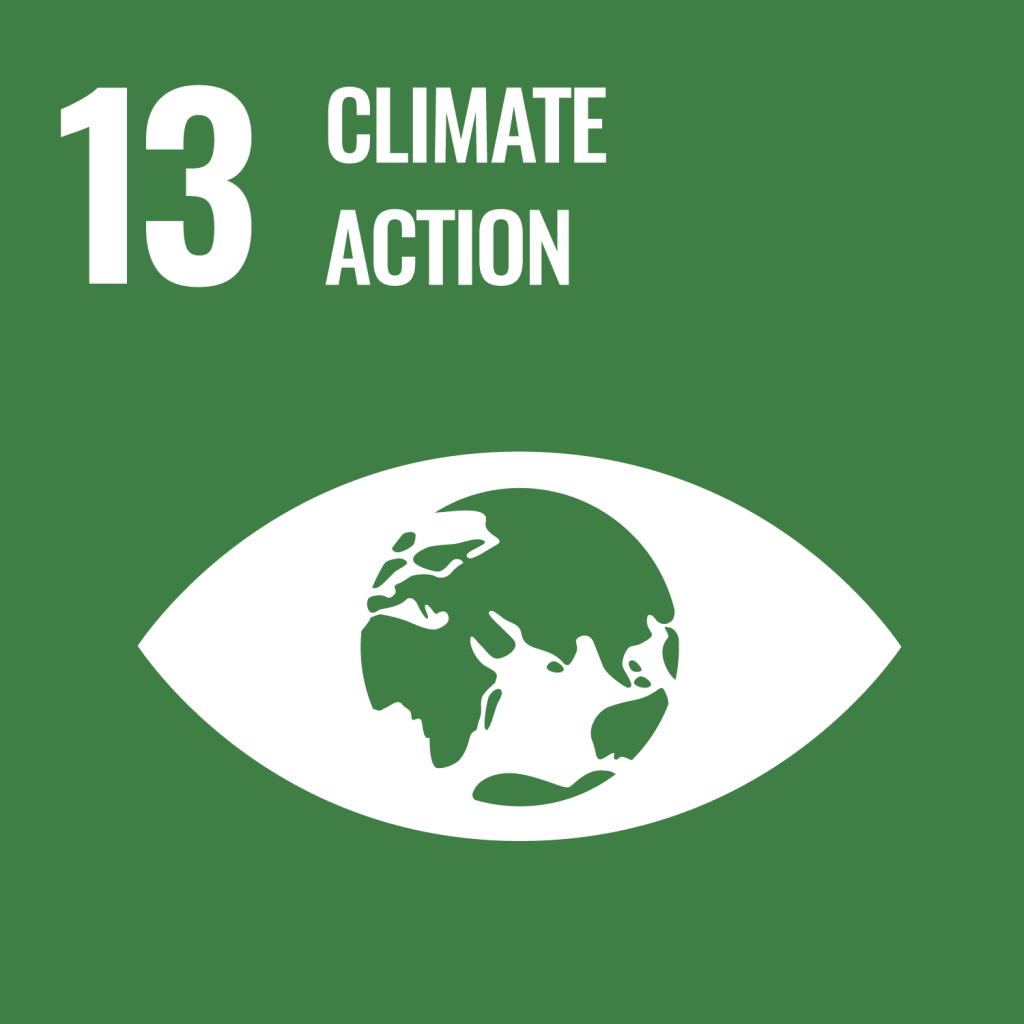
- Basic approach
- Targets and results
- Initiatives
- Strengthening resource recycling measures
- Acquire ISCC PLUS certification (internationally sustainable carbon certification)
- Participating in initiatives
Basic approach
Plastic is an indispensable material for modern society, but it is also associated with issues such as the problem of waste, depletion of natural resources, and its impact on climate change. Against this backdrop, in 2019 Resource Circulation Strategy for Plastics was formulated in Japan. The basic principles of 3R+Renewable *1 and ambitious milestones up to 2030 *2 were set out as directions to be taken. In order to accelerate these efforts, the Act on Promotion of Resource Circulation for Plastics was enacted in April 2022.
TOYOBO group handles a large number of plastic products, including films, which are our mainstay products. We recognize that the transition to a resource circulation society can be a major opportunity at the same time as business risks. In 2022, we clarified that our group can contribute to a recycling-oriented society under the Sustainable Vision 2030 and set targets for 2030. We will begin by promoting the use of green materials (biomass, recycled raw materials, volume reduction, and material conversion) from film-based *3.
Having adopted the slogan “Catalyzing Circular Economy,” Toyobo group is contributing toward the realization of the circular economy through a wide range of initiatives, and by fulfilling our responsibility to future generations, we are aiming to realize sustainable growth.
- 1 Streamlining (Reduce‧Reuse) the use of avoidable plastics. The essential use is switched to recycled materials and renewable resources (Renewable) and thorough recycling (Recycle).
- 2 Numerical targets from the perspectives of "Reduce," "Reuse ‧Recycle," and "Recyclable Use・Bioplastics." "Effective use of used plastics by 100% reuse by 2035, through recycling, etc." etc.
- 3 This excludes some products where safety or lifespan is an issue.
Targets and results
In May 2022, Toyobo group announced its Sustainable Vision 2030, which outlines its aspirations for the year 2030.
In this vision, we set a target of ratio of green materials in main business operation for 60% in 2030.
Through this greening, we will contribute to reducing the use of petroleum-derived resources and making them alternative.
Item | FY2031 Targets | FY2024 Results |
---|---|---|
Percentage of green films*
|
60%
|
13%
|
- Quantity ratio
Initiatives
Since the 1990s, our group has been engaged in recycling and the use of biomass raw materials, and has accumulated a variety of technologies and know-how. Going forward, we will aim to realize circular economy from 3R+Renewable perspective.
The following is an overview of initiatives from each viewpoint.
The goal of "green" is to replace products that incorporate the following perspectives.
Our Group-wide Efforts for the Life Cycle of Plastics and resource circulation / resource recycling
Reduce
We reduce the amount of raw material used by reducing thickness while retaining strength and functionality. When these kinds of materials are used by customers, packaging can be simplified and the amount of packaging materials used in the final product can be reduced.
- HARDEN®DN036
- SPACECLEAN®
We are reducing the amount of raw materials used while increasing recyclability by replacing previous products consisting of several different materials with those using a single material while maintaining strength and functionality.
- ECOSYAR® VP Series
- PYLEN EXTOP®
Reuse ⁻Recycle
We collect scrap materials generated in the manufacturing process (originating from airbags and film products) and reuse them as materials for products in the same and other categories. In doing so, we reduce waste generated in the production process.
In addition to the manufacturing processes of our group, we also implement initiatives to advance recycling in the manufacturing processes of our customers.
- ECOKURELEAF®
- ECOVYLOPET®
- COSMOSHINE SRF®
- Resource Recycling Project (KAMISHINE NEO® release film)
We proactively develop and market products made of used plastics as raw materials. We have also developed and are marketing TOYOBO GS Catalyst®, a polymerization catalyst for PET resin designed to make resin recyclable after polymerization reactions.
Through efforts centering on the PET material to which this technology is applied, we are advancing the expansion of material recycling technologies and materials in the global market.
- Material recycling: The reuse of used plastics as resins (raw materials) after they are pulverized or melted
- ECHORCLUB®
- Crisper®
- TOYOBO GS Catalyst®
- ReCrysta™
- Licensing of technology to Indorama Ventures Public Company Limited
In developing and practically applying chemical recycling technologies, we seek out technologies from around the world and collaborate proactively with external organizations and companies.
For example, we participate in the R Plus Japan project, actively pursuing development of chemical recycling technologies for converting recycled plastic into raw material for the production of high-quality recycled plastic.
- Chemical recycling: The reuse of used plastics after chemically breaking them down into crude raw materials
- R PLUS JAPAN
- Anellotech, Inc.
- Japan Chemical Industry Association
Renewable
By reducing CO2 emissions and reliance on petroleum-derived resources, biomass raw material is expected to serve as a climate change mitigation measure.
Our group is working for the conversion and expanded use of biomass raw materials, and for the practical application of biomass plastics that remain highly functional.
- BIOPRANA®
- VYLOAMIDE®
- HOLLOSEP®
- Polyethylene furanoate (PEF)
resin (under development)
- PEF Resin Partnership (Avantium)
- Partnership for PET resin made using 100% plant-derived raw materials (Suntory group and Anellotech)
- Japan BioPlastics Association
- THE JAPAN PLASTICS INDUSTRY FEDERATION
Other Initiatives
Waste reduction
To help reduce marine plastic waste, we participate in the Clean Ocean Material Alliance (CLOMA) established in Japan, as well as other initiatives in our efforts to develop and advance alternative materials.
- CLOMA
Examples of initiatives
Reduce
Contributing to the reduction of plastic use in packaging by making thinner and using a single material Reduce
In line with Japanese policies such as the "Plastics resource circulation / resource recycling Strategy," demand is increasing for film-based products that contribute to reducing the use of plastics in packaging materials and making them suitable for recycling. However, packaging materials such as foods that require a variety of performance, such as heat resistance and processing suitability, are generally designed by laminating several materials that have distinct characteristics. As a result, the number of raw materials used increased, and it was difficult to separate them separately. As a result, recycling was difficult.
Our film-forming and other techniques have been cultivated over many years to enhance the rigidity and functionality of biaxially oriented ※1 polypropylene (hereinafter referred to as "OPP") film, which is a single material, making the film 20% ※2 thinner than conventional composites.
In addition, the unique vapor deposition processing has enabled us to achieve both high-heat resistance and high-barrier properties, which have been considered difficult with OPP films.
We are working to reduce the volume of packaging materials by replacing them with new OPP films, and to contribute to the realization of a recycling-oriented society by promoting the use of materials.
- 1 Extending the film in two axial directions (vertical and horizontal) during film formation
- 2 For the PYLEN EXTOP® series of ultra-high-rigidity OPP films
Reuse ⁻Recycle
Shrink labels that use the same components (monomers) as PET bottles Material recycling
ReCrysta™ is an eco-friendly film and can be manufactured using over 50% materials sourced from recycled PET resins. It avoids the use of monomers*1 found in traditional PET films for shrink labels, opting instead for the same constituent monomers found in PET bottles. Until now PET films for shrink labels using conventional monomers have to be sorted separately from PET bottles, because such monomers compromise the properties of recycled PET bottles. On the other hand, PET films for shrink labels using ReCrysta™ that contains the same monomers as PET bottles, eliminate the need for separate sorting when producing PET resin flakes for recycling*2, thus enhance recyclability.
In 2024, based on third-party testing results of the PET film manufactured using ReCrysta™, APR determined that the product meets or exceeds the strict guidance criteria of the Critical Guidance Recognition pathway, enabling it to receive the APR recognition.
- 1 Neopentyl glycol, cyclohexanedimethanol, etc.
- 2 Use of film with ink removed
- 3 The Association of Plastic Recyclers
Material recycling of label boards
In KAMISHINE ® series of polyester-based synthetic papers made from recycled plastic bottles, we have developed a new recycling technique for KAMISHINE NEO® release film, which is used in label mount (release film/separator) applications.
Until now, the label base paper is often made of paper coated with resin or the like on the surface, and it has been difficult to recycle the material because it is a composite material of resin and paper. In the process of attaching labels to products, the label backing after the surface substrate (seal) was peeled off was generally discarded incinerated.
In 2022, we developed a new technology to produce the "KAMISHINE ®" series. This technique uses the label backing paper (KAMISHINE NEO® release film) after use as part of the raw material to produce the same performance as conventional products.
Resource Recycling Project was launched under the initiative of NEION Film Coatings Corp. a comprehensive manufacturer of adhesive film ⁻ coating technology, in order to implement resource circulation initiatives using this product and technology.
KAMISHINE NEO® Release Film for Label Backing Paper
Entire label structure (image)
Resource Recycling Project
Replace the label backing with film (KAMISHINE NEO® release film) and collect used label backing from customers. Efforts began in 2022 to recycle the collected used label backing as a raw material for film and recycle it as a resource. Since resource recycling initiatives are limited in the case of companies on a non-consolidated basis, they are being promoted through collaboration among companies in different industries with the expertise of their respective field.
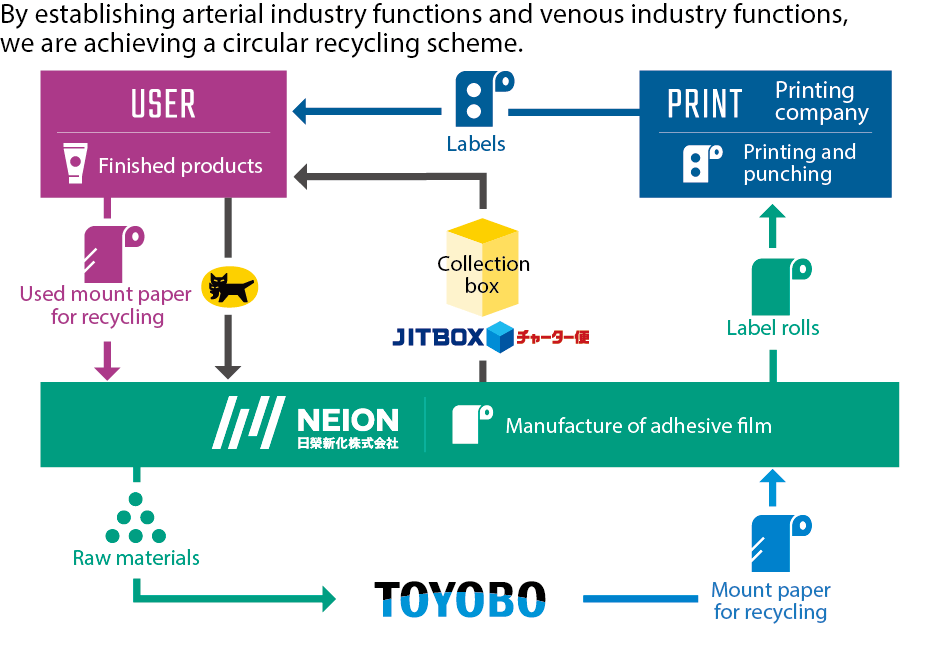
For more information about the Resource Recycling Project, please click here.
Development of the catalyst that can increase the recyclability of PET Material recycling
TOYOBO GS Catalyst®, a polymerization catalyst developed by Toyobo, is the world's first aluminum catalyst that does not contain any heavy metals. PET degrades (e.g., molecular weight loss, yellowing.) during repeated melting processes in recycling, but the PET obtained using this catalyst does not deteriorate when melted, making it well suited to recycling.
In December 2022, we received the 71st Chemical Technology Award in fiscal 2023 from the Japan Chemical Association, the largest chemical society in Japan, for developing and industrializing this polymerization catalytic converter. This award is awarded to those who have achieved particularly remarkable achievements in Japan's chemical industry.
In 2024, the catalyst received certification for recycling performance (“APR Design® for Recyclability”) from The Association of Plastic Recylers (APR), the international trade association for plastics recycling.
Toyobo has already licensed the technology to Thailand's Indorama Ventures Public Company Ltd., the world's largest PET resin manufacturer. Toyobo also participated in The Packaging Conference 2022, an international conference which held in America, and held exhibition and presentation. With the excellent recyclability of the produced PET resin, we will contribute to realize the circular economy in cooperation with Indorama.
- Toyobo promotes global use of its aluminum catalyst technology through polymerization technology licensing contract with world’s largest PET producer, Indorama Ventures Pcl
- Toyobo wins Chemical Society of Japan Award for Technical Development for 2022; helping realize a circular economy with an eco-friendly aluminum catalyst for polyester polymerization
- TOYOBO GS Catalyst®, an eco-friendly aluminum catalyst for polyester polymerization, receives recognition for APR Design® for Recyclability
TOYOBO GS Catalyst® (front) enables synthesis of resins with higher transparency than other catalysts
PET bottles synthesized using TOYOBO GS Catalyst®
Recycling of used plastics beyond the industry Chemical recycling
in June 2020 the joint venture company R Plus Japan, Ltd. was established by a group of 12 companies operating in Japan's plastics value chain, which includes Toyobo. As of September 2024, this number has grown to 45 companies, and together with Anellotech it is continuing with the development of new technologies.
Anellotech's recycling techniques
Anellotech's new technology is a chemical recycling technology that uses used plastics as raw materials to produce crude raw materials for common plastics. It is characterized by the ability to produce a variety of crude raw materials from the mixed state of multiple types of plastics, and by the low loss in the process. Because it can be processed by fewer processes than the conventional method, it is expected to reduce CO2 emissions and energy-consumption. If this technology is established, it is possible to return used plastics, which have been used in heat, to raw materials, and it is possible to add more value to used plastics.
So that we can contribute to solving the common worldwide problem of plastics, we aim to have this technology in practical use by 2030. To do this, we are collaborating with companies in a range of industries, including those in sorting and processing of collected plastics, distribution, and production of monomers, polymers, packaging and containers, and beverages.
Renewable
100% biomass plastic in film Biomass feedstock
Our focus is on furandicarboxylic acid (FDCA) as a biomass raw material. FDCA is polymerized using our proprietary technology to produce polyethylene furanoate (PEF), a high-performance polyester. PEF is a 100% biomass plastic with excellent gas barrier properties, and when formed into a film can help extend the shelf life of food contents, and thus reduce food losses. The world's first FDCA production plant is scheduled to be opened by Avantium. We plan to use this FDCA to produce PEF film.
Polymerization of 100% bio-based PET resin Biomass feedstock
In December 2021, Suntory Group and Anellotech, Inc. jointly developed a prototype PET bottle made from 100% plant-derived raw materials. Toyobo contributed to the development through its polymerization technology.
Waste reduction Initiatives Minimizing waste
Our manufacturing sites are working under TOYOBO Group Fundamental Policy on the Global Environment to reduce, reuse, and recycle waste. We strive to minimize the amount of landfill waste by reducing the amount of waste generated by reusing non-standard products and scrap materials, and by making the most effective use of waste generated.
Strengthening resource recycling measures
Renewable-resource business development
In April 2020, we established Renewable Resources Business Development Department in order to further accelerate our efforts related to plastic resource circulation and contribute to a sustainable society.
Renewable Resources Business Development Department is searching for technologies and collaborating with other companies to promote the conversion to biomass raw materials and the use of recycled raw materials.
We have drawn up a roadmap to 2030 — while also looking towards 2050 — based on government policies in Japan and overseas, as well industry targets for the environment. In collaboration with our partners worldwide, we aim to shift to biobased products focused on polyester resin, and to establish technologies related to mechanical and chemical recycling. Working closely with each Solutions Division, we will also adapt flexibly to changes in the business environment.
Mission
Long-term outlook
Acquire ISCC PLUS certification (internationally sustainable carbon certification)
Toyobo Co., Ltd. and Toyoshina Film K.K., a Toyobo Group company, have received ISCC (International Sustainability and Carbon Certification) Plus certification, an international certification designed to confirm the sustainable content of products. The properties of bio-based raw materials in the OPP film to be manufactured by Toyoshina Film will be assigned to a portion of the product based on the mass balance approach*.
ISCC Plus certification, which is part of the ISCC certification system, is aimed at confirming that mainly bio-based feedstocks and recyclables are properly managed in the process of turning raw materials into final products in the entire supply chain using the mass balance approach.
- A method in which during the process of turning raw materials into final products and the distribution process, raw materials with certain properties (e.g., bio-based raw materials) are mixed with raw materials that do not have the properties (e.g.,petroleum-based raw materials); the properties are thus assigned to a portion of the product according to the input of the raw materials having those properties. (Source: Ministry of Environment, “Roadmap for Bioplastics Introduction.”)
Participating in initiatives
The Toyobo group is working closely with a variety of companies and organizations, and is active in a number of initiatives aimed at contributing to the construction of a plastics value chain that is appropriate to the era of the circular economy.
Japan BioPlastics Association
This group was established in 1989 with the aim of promoting the use of bioplastics,* and establishing a testing and evaluation system. An executive from Toyobo serves as the Vice Chairman, and we are active in the association's activities including participation in executive meetings and various committees.
- Collective term for biodegradable and biomass plastics
CLOMA (Clean Ocean Material Alliance)
CLOMA is an organization established in Japan with the aim of increasing the effective use of marine plastic waste through reductions and recycling. Its members include more than 350 companies throughout the supply chain involved in the manufacturing, processing, and use of packaging and other materials. Toyobo has been a member of the alliance since it was established in 2019.
Through collaboration with other CLOMA members, which includes manufacturers, processors and users of packaging and other materials, we will work to develop and promote the use of alternative materials.
J4CE (Recycling Economic Partnership)
This partnership was founded for the purpose of strengthening public and private partnerships, with the aim of further fostering understanding of the circular economy among a wide range of stakeholders, including domestic companies, and promoting initiatives in response to the accelerating global trend toward a circular economy. We participated in J4CE in September 2022.
Circular Partners
Circular Partners (CPs) is an industry-government-academia consultative body launched by the Ministry of Economy, Trade and Industry to help realize a circular economy.
Circular Partners aims to create a vision, medium- to long-term roadmap, and information distribution platform for the realization of a circular economy in Japan through collaboration among industry, government, municipalities, universities, and business and industry organizations.
TOYOBO and TOYOBO MC participated in the project in 2023.
APR(The Association of Plastic Recyclers)
This is an international industry organization that represents the recycling industry for plastics. We are supporting circular economy through unique certification programs to ensure high-quality recycled plastics, testing methods to evaluate recyclability, and educational activities. We joined in March 2023.
CEFLEX (Circular Economy for Flexible Packaging)
In August 2019, Toyobo group joined the European consortium Circular Economy for Flexible Packaging (CEFLEX). Established in 2017, CEFLEX is a consortium that promotes the realization of a circular economy through the use of flexible packaging. This includes more than 130 companies and organizations involved in the flexible packaging value chain, including leading materials manufacturers and recycling companies. Its goals include establishing by 2025 a Europe-wide collection, sorting, and reprocessing infrastructure for used flexible packaging. While understanding the latest information and trends regarding recovery systems and regulations, we will focus on developing and supplying eco-friendly technologies and products to contribute to the realization of a circular economy.